The 5-Second Trick For Hydraulic Filter Press
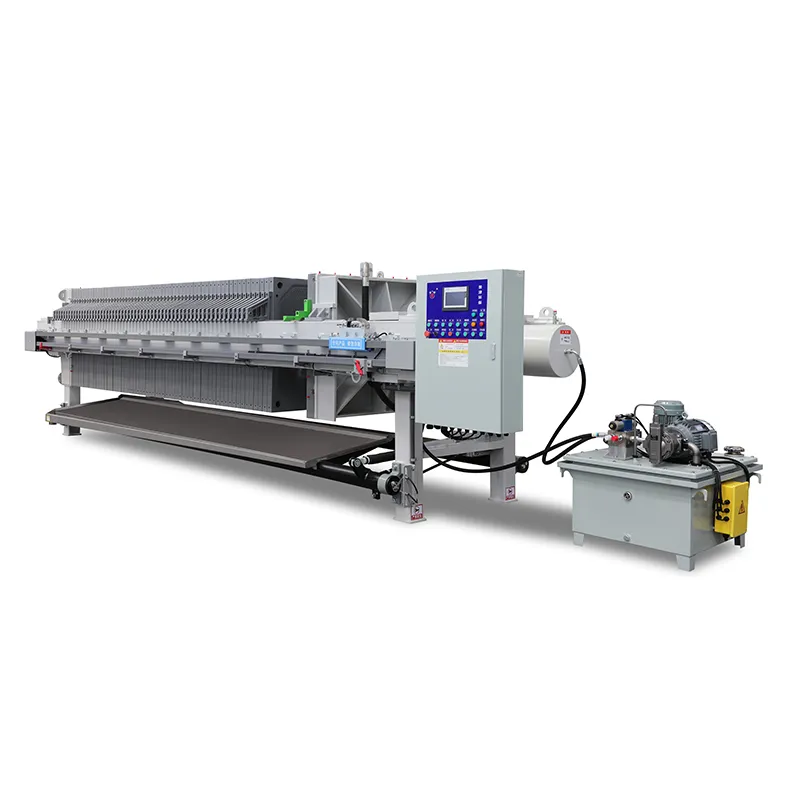
Implement a Preventive Upkeep Prepare: Standard servicing with the hydraulic system, filter plates, and also other parts can stop expensive downtime and extend the lifestyle of your filter press.once the pressing is concluded, the PLC will control the automatic unloading system to eliminate the filter cake over the filter cloth; throughout the whole method, the PLC will continually keep an eye on the equipment operation standing. As soon as an abnormal scenario is discovered, including overload, quick circuit, and so on., the fault alarm and self-protection system will be instantly activated to make sure the Safe and sound and secure Procedure in the equipment.
The cylindrical pip filtration surface area, pioneered by Edwards & Jones, offers a sixty% no cost drainage place at the rear of the filter fabric, and also extending the fabric lifestyle.
The stable development of a filter press, innovation in design and style, improved Vitality efficiency and growth options of automation modules bring on a steadily rising desire for filter press machines catapulting it into a basis unsurpassed by conventional dewatering procedures for solids.
Filtration: After the slurry is inside the filter press, pressure is placed on the system. This pressure is usually created mechanically or hydraulically. Since the pressure improves, the liquid percentage of the slurry is forced to pass through the filtering medium, leaving the reliable particles behind.
2. The liquid passes through the filter fabric, although the strong particles are retained over the filter cloth to form a stable filter cake.
DISCSTAR® H is the newest era of module housing. The specific horizontal stainless steel housing for sixteen filter modules, is formulated and created for everyday use.
If a larger capacity ingestion is necessary, the cylindrical spacer, and that is attached on the hydraulic cylinder as well as relocating pressure plate, may be eradicated quickly and easily. The filter press can Hence be supplemented by the extra filter plates. Even so, the most capacity growth will depend on the filter press architecture. We are going to be happy to recommend you on this.
The Superior design and style of your MDS causes it to be a self-cleaning unit due to friction no cost motion involving the rings, is relevant across a wide range of sludge concentrations (2000 mg/L 50000 mg/L), and is highly suited to oily sludge.
1.Enhanced Efficiency: Automation hastens the filtration process, permitting for faster cycles and higher throughput. This will drastically improve the productiveness with the Procedure.
Some filter presses have automatic cake removing mechanisms, while some need manforce to empty intervention. The discharged filter cake could be even more processed or disposed of as essential.
Moreover the filter press plates is usually customised to resist on the high temperature ailments and also to be also able to make cake washing and cake drying in an effort to raise the filtration efficiency.
You'll discover this quantity (possibly 5 or 6 digits) on the first site from the complex manual or about the name plate to the movable head on the filter-press
The respective drip plates are mounted under the plate pack. In addition, the shut drip plates especially drain off the cleansing water when cleaning the filter plates and filter cloths in the press. To vacant the filter press, the drip plates must be swung open (automatically) / taken off (manually) to show Filter Press the discharge chute to the filter cake.}